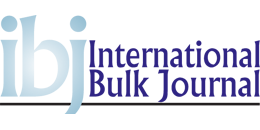

(Posted on 28/08/19)
It is a completely new approach to the plant, processes, and machinery of industrial mills. With Mill E3, Bühler revolutionizes the milling industry and sets new standards in cost-effective building investment, project realisation time, and energy consumption. “After the introduction of automation 40 years ago, Mill E3 is the next big step forward in milling,” says Johannes Wick, CEO of Grains & Food at Bühler Group. The first customer to rely on Mill E3 also uses Bühler blockchain technology to trace grain for more transparency and food safety.
For decades industrial milling concepts have focused on optimizing machines and processes, but the basic design concept remained the same, based on buildings with a minimum of five to six floors. With the completely new approach of the Mill E3, Bühler now optimizes the entire arrangement and construction concept. At the Networking Days 2019, Bühler shows that it is possible to build flour mills with latest technology more cost-effectively, install them quicker, and operate them with less impact on the environment.
Mill E3 stands for advantages on three efficiency levels: space, time, and energy. In the optimal case a Mill E3 building can be 30% smaller in volume than a traditional mill of the same size. The construction of the Mill E3 building not only locks up less capital, it is also completed more quickly. By using pre-assembled modules, Mill E3 is installed 30% faster than conventional flour mills. "It's basically a plug-and-play mill," says Stefan Birrer, Head of Business Area Milling Solutions. This means Bühler customers can set up their Mill E3s more quickly and start generating revenues faster. It significantly reduces infrastructure cost, construction time and complexity.
With the same output, Mill E3 reduces energy consumption by up to 10%, without compromising yield or quality. This is down to the compact mill design and innovative process solutions such as the newly developed integrated grinding system Arrius. Arrius has an integrated drive, which saves up to 10% of energy compared to conventional roller mills. The TUBO Tubular Push Conveyor replaces specific pneumatic transport passages in order to save energy. TUBO is much more efficient and makes food production even safer. The product is transported gently, loses no weight due to drying out, and the conveyor system is more hygienic because the pipelines are self cleaning.
"Be it space, time, or energy: On all these levels, we were able to show that the plant will be better than anything other mill builders have on the market," says Stefan Birrer. "The design, the new grinding system Arrius and the IoT and Blockchain applications are revolutionizing the milling industry once again," adds Johannes Wick. Bühler customers can order Mill E3 now.
The UK’s largest milling company, Whitworths Holdings Ltd. incorporating Whitworth Bros. Ltd. and Carrs Flour Mills Limited, operates 17 mills on 9 sites. It is the first company to rely on Mill E3. "Besides the obvious mechanical benefits E3 offers, we were also convinced of the digitalization approach. Bühler is definitely on the forefront in this respect," says Mike Peters, Managing Director of Whitworth Bros. Ltd. "For us, Mill E3 offers more than just a new technology approach. It will enable us to create complete transparency for our customers in the future," he adds. Together with Mill E3, Bühler has proposed increasing transparency along the value chain by adding connectivity features, digital services, and blockchain to help guarantee the end product quality.
Bunge Global SA has confirmed that it has completed the previously announced sale of its North America... Read more
Following the successful debt raising at the end of April 2025, SSAB has secured an additional EUR 430... Read more
Despite China’s dominant position in securing commodities across Africa, there are still many... Read more
Rio Tinto and Hancock Prospecting will invest $1.61 billion (Rio Tinto share $0.8 billion) to develop... Read more
SSAB has commenced preparatory work to build a new, state-of-the-art steel mill in Luleå, Sweden... Read more
Anglo American plc has streamlined its executive leadership team to reflect substantial progress with... Read more
NeoSmelt, a consortium of leading resources, energy and manufacturing companies working together on... Read more
Northern Ireland based Telestack have announced that they have been awarded a contract for the supply... Read more
Bühler has opened its new Puffing Application Center in Uzwil, Switzerland, providing food... Read more
Rio Tinto is investing CA$7.6 million in an industrial demonstration project to assess the integration... Read more