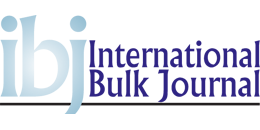

(Posted on 22/05/24)
Bruks Siwertell has launched new digital advances designed to enhance the safety and efficiency of dry bulk handling operations. They are available as optional extras on new and existing large-scale Siwertell ship unloaders and loaders.
Included in this latest package of developments is a radar-based anti-collision system, which enables supervised, semi-automatic unloading and a further option of digital hatch visualization. Bruks Siwertell already offers a laser-based anti-collision system, which also has the option for semi-automatic unloading.
“We are developing systems on a continual basis,” says Krister Holmberg, Manager Electrical Systems, Bruks Siwertell. “Digital advances are offering new levels of operational insight, and safety improvements, including the efficiency advantages of being able to run the ship unloader or loader in a semi-automatic mode when our anti-collision systems are in use.
“Unloading and loading operations should always be supervised, at all times, but when the anti-collision system is activated, the PLC is able to take control of the movements and follow a pre-defined sequence, which can enhance the efficiency of the operation. To be able to use this function, on a ship unloader for example, the program for automatic reduction of the speed on the traveling, slewing and pendulum must be activated,” Holmberg explains.
The radar-based system uses technology from a third-party company. It has extensive experience in the development of industrial radar applications and extends this expertise to original equipment manufacturers (OEMs) by providing interface options.
The use of radar offers some distinct advantages in dry bulk handling. Even in challenging environmental conditions such as dust, fog, and snow, it is able to provide a very effective mechanism for digital image generation.
With the radar-based anti-collision system, along with the option for data-generated hatch visualization, it is possible to see the hatch and the material inside, with top, side, and overall views available.
The operator can also see the distances in meters to the hatch coaming and the depth of the bulk material in the hold, making it much easier to make operational decisions in either manual or semi-automatic modes.
Bruks Siwertell Group has announced a leadership transition as Peter Jonsson steps down as CEO after... Read more
ClassNK has issued an approval in principle (AiP) for a Rigid Windsail Type Wind-Assisted Propulsion... Read more
Elcome International’s new high-speed internet service, WELCOME, is revolutionising the way ship... Read more
Kaiko Systems, a leader in AI-driven frontline intelligence for the maritime industry, today announced... Read more
Marcegaglia’s latest acquisition, the LHM 600, marks a significant milestone as the 2,000th mobile... Read more
The Isle of Man Ship Registry (IOMSR) is playing a key role in the development of a high-tech sail aimed... Read more
AtoB@C Shipping, subsidiary of ESL Shipping, has taken delivery of Terramar in Goa, India on 14 March... Read more
As a new strategy period commences, VIKING Life-Saving Equipment A/S has achieved strong financial results... Read more
Baltic Exchange has introduced a series of green fuel options to its FuelEU voyage and compliance cost... Read more
Veson Nautical, a global leader in maritime data and freight management solutions, and Cargill have... Read more