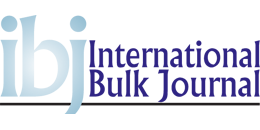

(Posted on 08/05/19)
Subsea Industries has won the Arctic Innovation Award 2019 for its Ecospeed non-toxic hull coating. The winner of the award was announced at the Arctic Shipping Forum held at the Paasitorni Congress Centre in Helsinki, Finland.
According to the organizers the panel of independent judges, consisting of leading Arctic specialists, gave the award to “the company or individual that has developed the most innovative new technology, environmental practice or service to benefit the Arctic region.”
About the award Subsea Industries CEO Boud Van Rompay said: “We are very proud to have been given this award by important members of the Arctic shipping community. This recognition strengthens us to keep pursuing our goal of clean rivers, seas and oceans.”
A short summary of the winning entry:
No repaint needed after 10 years sailing in ice
The number one consideration in a hull coating for ice-going vessels and icebreakers is the ability of the coating to protect the hull in the harshest marine environment there is.
Experience has shown that Ecospeed stays on the hull longer and resists the ice far better than the most generally used specialized ice coatings. Ecospeed remains bonded to the ship’s plates even as they flex and bend under ice pressure and impact.
Ecospeed has been recognized by Lloyd’s Register as an abrasion resistant ice coating for ships. Its correct use on the ice belt specifically permits a reduction of the ice belt’s steel plating by up to 1mm.
An ice-going hull coating must have low friction characteristics in order to be fuel efficient. But it is not enough for the hull to be smooth and have low friction at launch. It must stay that way for the life of the vessel. Ecospeed will hold up and will not be damaged in the ice and so will remain smooth for the life of the vessel, thus saving fuel. Even if minor repairs are needed in drydock the original quality of the coating remains intact.
Applying Ecospeed is a simple process which can be carried out using the usual spray equipment without tenting and heating. Only two coats of 500μm each are required. Minimum overcoat time is a few hours and there is no maximum, making it easy to fit into your drydock or new build schedule.
Alfa Laval has completed the acquisition of UK-based NRG Marine, a leading provider of ultrasonic anti... Read more
In a landmark moment for the global maritime industry, the Maritime Battery Forum (MBF) and the Zero... Read more
Bruks Siwertell Group has announced a leadership transition as Peter Jonsson steps down as CEO after... Read more
ClassNK has issued an approval in principle (AiP) for a Rigid Windsail Type Wind-Assisted Propulsion... Read more
Elcome International’s new high-speed internet service, WELCOME, is revolutionising the way ship... Read more
Kaiko Systems, a leader in AI-driven frontline intelligence for the maritime industry, today announced... Read more
Marcegaglia’s latest acquisition, the LHM 600, marks a significant milestone as the 2,000th mobile... Read more
The Isle of Man Ship Registry (IOMSR) is playing a key role in the development of a high-tech sail aimed... Read more
AtoB@C Shipping, subsidiary of ESL Shipping, has taken delivery of Terramar in Goa, India on 14 March... Read more
As a new strategy period commences, VIKING Life-Saving Equipment A/S has achieved strong financial results... Read more