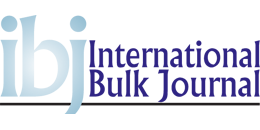

(Posted on 18/10/19)
DNV GL’s is continuing long-standing efforts to ensure safe performance of aft most propeller shaft bearings. The class society has recently updated its oil lubrication acceptance criteria to differentiate between environmentally acceptable lubricants (EALs) and mineral oils in terms of their ability to form a reliable lubricant film.
In recent years an increasing number of costly stern tube bearing failures have been reported across multiple ship segments and sizes. These failures have coincided with the increased uptake of environmentally acceptable lubricants (EALs) after the December 2013 introduction of regulations prohibiting the use of mineral oils in all oil-to-sea interfaces on board commercial vessels trading in U.S. waters. Many of the failures are wiping damages at the aft end of the aft stern tube bearing occurring with fresh oil. While the majority of the breakdowns were caused by a combination of factors, the performance of the lubricants themselves has been drawn into question by the industry.
To better understand how EALs perform compared to traditional mineral oils commonly used in stern tube bearings, DNV GL initiated a joint development project together with the marine insurers The Swedish Club, Norwegian Hull Club, Skuld and Gard (1). The aim of the project was to map out potential differences between the lubricants’ physical properties that determine their oil film load-carrying capacities, with a focus on how the lubricant viscosity is influenced by parameters such as temperature, pressure and shear rate. Operational issues and potential long-term degradation issues have not been covered by the study as the majority of the observed failures occurred with fresh oil. Laboratory testing has been carried out by and under the guidance of leading tribology experts at the University of Sheffield in the UK and at INSA Lyon in France.
In order to decide which influence parameters to focus on when investigating EALs, it is essential to understand the major factors that affect the performance of an aft stern tube bearing. “The physical forces acting on propeller shafts under highly variable vessel-operating conditions result in a complex array of challenges that must be overcome to achieve a satisfactory shaft alignment and ensure adequate lubrication of the aft stern tube bearing,” explains Øystein Åsheim Alnes Principal Engineer, at DNV GL Group Technology and Research. “Over the past years several EEDI-driven vessel design features have helped improve overall vessel energy efficiency but have had an unwanted secondary impact: there is no doubt that bigger and slower-rotating propellers tend to reduce the safety margins of the aft stern tube bearing. Likewise, various hull and propeller wake optimization features have been found to do the same for certain operating conditions. As the maritime industry works towards achieving IMO’s ambitious goals for reducing its environmental footprint, this trend towards more energy-efficient ships needs to continue. Therefore, we at DNV GL have acknowledged that a more sophisticated approval methodology for stern tube bearings is required.” The industry-standard approach of only evaluating the bearing projected pressure and the simplified shaft vs bearing relative slope for static conditions is no longer adequate.
DNV GL has built unrivalled expertise in this field over decades, merging knowledge from class, independent advisory projects and dedicated research and development activities. This accumulated know-how has enabled the classification society to develop state-of-the-art design rules for shaft alignment, including a highly detailed approach to verify the aft stern tube bearing design for both static and running conditions. The calculation method for the minimum shaft-rotational speed at which hydrodynamic lubrication of the aft stern tube bearing is ensured was introduced in 2013. Better known as the “DNV GL oil lubrication criteria”, it is based on a quasi-empirical solution of the Reynolds equation for journal bearings. It accounts for the challenging conditions that are typical for stern tube bearings, such as very uneven load distribution and extensive misalignment between shaft and bearing. The calculation method aims to ensure hydrodynamic lubrication in the areas exposed to the maximum bearing pressure, setting a limit for the minimum allowable continuous operational shaft speed at dead slow ahead and engine maximum continuous rating.
The International Maritime Organization (IMO) has confirmed the expansion of the data reference model... Read more
The SEA-CARE working group concluded its third session in February by confirming commitments to share... Read more
Torvald Klaveness has announced the decision to consolidate all digital services under Klaveness Digital... Read more
The International Association of Dry Cargo Shipowners (INTERCARGO) has renewed its call for straightforward... Read more
The Swedish Club has delivered strong results for 2024, posting a USD 34 million profit and significantly... Read more
In line with NORDEN’s positive long-term outlook for Capesize freight rates, the company have... Read more
OrbitMI, a global provider of maritime software and data products, has expanded its workflow capabilities... Read more
Current ClassNK Senior Vice President Hayato Suga has been appointed as President & CEO as well... Read more
The surge in demand for Cape Size bulk carriers will continue for another six weeks, driven on by increased... Read more
OrbitMI, a leading provider of maritime SaaS software, has announced that Istanbul-based Statu Shipping... Read more