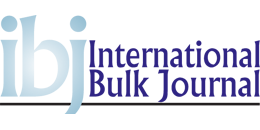

(Posted on 13/09/21)
During a visit to ArcelorMittal Germany’s steel plant in Hamburg, Federal Environment Minister Svenja Schulze pledged the Federal Government’s support for the construction of Germany’s first industrial scale hydrogen-based direct reduced iron (DRI) plant.
This demonstrator plant, which will use hydrogen exclusively as the chemical agent to reduce iron ore into DRI, is intended to lay the foundation for a steelmaking process that means steel can be produced with zero carbon-emissions[1>, using electric arc furnaces fed with hydrogen reduced DRI and scrap metal, powered by renewable electricity.
The Federal Government has expressed its intention to provide €55 million of funding support towards the construction of the plant, which is half of the €110 million total capital expenditure required. The next step is for the European Commission to approve the Federal Government's intention to provide funding before the installation of the new plant can begin. Production is scheduled to start in 2025.
DRI is currently produced using natural gas to reduce iron ore. In a transition phase, the process of reducing iron ore with hydrogen will first be demonstrated using hydrogen generated by the separation of waste gas from the Hamburg plant. Once available in sufficient volumes and at an affordable price, green hydrogen - made from the electrolysis of water using renewable energy - will be used. By 2030, ArcelorMittal plans to produce more than one million tonnes of zero carbon-emissions steel a year in the Hamburg plant alone, thereby saving around 800,000 tonnes of CO2 emissions annually.
The plant is an important component of ArcelorMittal Germany’s Steel4Future strategy, which involves the conversion of its four German plants - in Hamburg, Bremen, Duisburg and Eisenhüttenstadt - to zero carbon-emissions steel production in the coming years.
Commenting, Dr. Uwe Braun, CEO ArcelorMittal Hamburg, said: “With the intended plant, for the first time we will be able to produce 100,000 tonnes of DRI for steel production using hydrogen - as early as 2025. Our project thus contributes to the goal of greenhouse gas reduction and a low-carbon economy. The technology is also directly transferrable and shows how other steelworks in our group – like Bremen and Eisenhüttenstadt - can convert to zero carbon-emissions steel production processes. But one thing is clear - the production of low or zero carbon-emissions steel is significantly more expensive than traditional steelmaking methods. When it comes to these challenges, we continue to rely on political support to create the appropriate framework conditions. The German Government's intention to provide funding helps our project and we are very grateful for this. Now we need approval from the European Commission so that words can be followed up with action.”
ADM and Mitsubishi Corporation have signed a non-binding memorandum of understanding to form a strategic... Read more
ESL Shipping and global steel manufacturer SSAB have agreed on a multi-year extension of the agreement... Read more
Anglo American’s Sakatti copper and polymetallic project in Finland has been designated as a &... Read more
FEFAC, representing the EU compound feed and premix manufacturers, noted with deep concern the announced... Read more
Catering to the growing demand from India’s confectionery, infant formula, and dairy sectors,... Read more
Khalifa Economic Zones Abu Dhabi – KEZAD Group, the largest operator of integrated and purpose... Read more
Rio Tinto will invest $1.8 billion1 to develop the Brockman Syncline 1 mine project (BS1), extending... Read more
Catherine Cobden, President and CEO of the Canadian Steel Producers Association (CSPA), has released... Read more
Enough domestic ferrous scrap is available for electric arc furnace (EAF) steelmakers to supply nearly... Read more
Cargill’s Ocean Transportation business and leading tanker shipping company, Hafnia, have joined... Read more