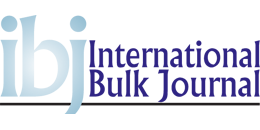

(Posted on 11/03/19)
When it comes to coal, the United States is one of the world leaders in exports and production. The United States produced 753.7 million short tons in 2018, and exported more than 116 million short tons, according to statistics from the U.S. Energy Information Administration. Only China produced more coal than the United States, according to industry statistics.
After several years of decline, U.S. production increased in 2017 for the first time since 2013. Much of the U.S. coal is exported to Asia, which accounts for close to 80 percent of total global coal usage. In China, roughly 70 percent of the energy consumed is obtained from coal. India also imports high volumes of coal, as 75 percent of the country is dependent on coal-based electricity. About 19 percent of U.S. coal exports go to India, while 33 percent are shipped to Europe and 9 percent to Japan, according to Bloomberg.
Even in the United States, coal is still the main source of power in 18 states and supplies almost 30 percent of American power, Forbes said in an article in 2018.
While there is a worldwide trend toward renewable energy, coal is still very much an important part of the global economy. The landscape might be changing, but the demand for coal is still surprisingly strong. The International Energy Agency said global demand will remain essentially stable through 2023.
Lamberts Point Coal Terminal in Norfolk, Virginia stands at the heart of U.S. coal production. The terminal has an annual throughput capacity of 46 million tons. The terminal’s backbone is its powerful Pier 6, where one-third of the nation’s coal exports are transloaded. The pier is capable of loading 8,000 tons per hour, and operates 24 hours a day, seven days a week.
Two critical bulk loading cranes at Pier 6 include energy chains manufactured by igus, a Germany-based manufacturer of motion plastics. The energy chains are maintenance and lubrication-free, and the company’s newly-introduced P4.1 system can achieve a service life of 20 years or 30,000 trolley hours. “The pier has been around for 50 years, but the infrastructure is constantly being updated,’’ said Ervin Mullins, a former Senior Pier Master at Pier 6. “It’s going to be around for another 50, I’m pretty sure.”
Energy chains from igus have been used in coal loading facilities from British Columbia to Rotterdam. The reliability, durability and infrequent maintenance have played an important role in the decision of many crane engineers to choose igus products.
Energy chains from igus have been serving the crane industry for 30 years. E-chains are capable of operating at trolley speeds up to 2,000 feet per minute and travel distances of 2,600 feet. No additional motors on controls are required for long travels, and roller chains allow for a significant reduction in required drive force. Energy chains also require about 50 percent less cable length.
Jeff Johnston, the Crane Maintenance Manager at the Port of Virginia said there was concern over durability and performance when his team chose to use igus energy chains. He learned quickly that the energy chains were the best choice.
“In the first year they were in service, we were waiting for something major to go wrong,’’ Johnston said. “It just didn’t happen. The maintenance we had to do was minimal compared to the maintenance we had to do with the wheeled festoon systems.”
“The system provides a better service to our operational colleagues, to get their work done in a timely fashion and meet their metrics as well. It’s a maintenance-friendly system compared to a festooned system,” added Danny Webb, the Port of Virginia’s general manager of technical support.
Wheeled festoons have been used in bulk shipping ports for years as cable management systems for the trolley power and communication supply. But festoon systems often could not stand up to the harsh environmental conditions, leaving cables swinging, tangling and breaking, and forcing port crew members to repair systems as quickly as possible in extreme weather.
“We were a wheeled festoon port for years,’’ Johnston said. “Bearings, bolts, shock cables, tow cables – all of those components need to be maintained monthly and replaced quite often. When we switched to the energy chains, all of that stuff went away.”
“One of the unique features of the energy chain system is the cables move only when the trolley is moving,’’ added Sean McCaskill, the Engineered Systems Manager for igus North America. “In comparing a festoon system to an energy chain system, in windy conditions the cables will be swinging in the wind, putting mechanical stresses into cables, work hardening the conductors and propagating a system failure. If you raise the winds higher, to a storm environment, such as a hurricane, energy chains will be able to guide and protect cables. There’s nothing to swing in the wind. The entire energy chain system is fully supported in a steel guide trough that is connected directly to the crane girder.”
The igus energy chains at Lamberts Point are included on two 18-story high ship loaders that permit the facility to load two cape-size bulkers simultaneously. The tandem rotary dumpers feed the ship loaders for a combined dumping capacity of 8,000 tonnes per hour.
With a 24/7 operation schedule and customers worldwide depending on coal, there is little margin for error and unplanned downtime at Lamberts Point. Ports everywhere strain to keep up with demand in the global marketplace. That’s why the dependable igus energy chains are such a critical part to operations.
Bruks Siwertell Group has announced a leadership transition as Peter Jonsson steps down as CEO after... Read more
ClassNK has issued an approval in principle (AiP) for a Rigid Windsail Type Wind-Assisted Propulsion... Read more
Elcome International’s new high-speed internet service, WELCOME, is revolutionising the way ship... Read more
Kaiko Systems, a leader in AI-driven frontline intelligence for the maritime industry, today announced... Read more
Marcegaglia’s latest acquisition, the LHM 600, marks a significant milestone as the 2,000th mobile... Read more
The Isle of Man Ship Registry (IOMSR) is playing a key role in the development of a high-tech sail aimed... Read more
AtoB@C Shipping, subsidiary of ESL Shipping, has taken delivery of Terramar in Goa, India on 14 March... Read more
As a new strategy period commences, VIKING Life-Saving Equipment A/S has achieved strong financial results... Read more
Baltic Exchange has introduced a series of green fuel options to its FuelEU voyage and compliance cost... Read more
Veson Nautical, a global leader in maritime data and freight management solutions, and Cargill have... Read more