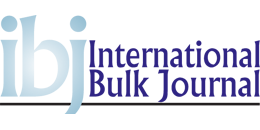

(Posted on 22/05/20)
The final vessel in a series of five ship-assist tugs has been successfully converted to Thordon’s RiverTough tailshaft bearings and TG100 shaft seals and has returned to work on the Mississippi River.
These five tugs are considered to be the first ship-assist tugs operating in the lower Mississippi fitted with both RiverTough bearings and TG100 seals.
The New-Orleans-based tug operator converted its first vessel – a 117ft (35m), 4200hp twin-screw ship-assist tug – in 2015 to reduce the operating and maintenance costs associated with traditional rubber tailshaft bearings and clad welded journals.
According to Thordon Bearings’ Sales Manager, Jim Bright, who was involved in all five retrofits, the owner specified the solution because it was tired of unbudgeted costs following frequent premature bearing and shaft wear. The owner was familiar with the reputation of RiverTough bearings and its performance on other workboats.
“Their previous arrangements of rubber bearings had to be replaced every two years or so and the shafts needed to be repaired due to excessive wear. This can be avoided with Thordon’s products,” said Bright.
When RiverTough bearings are used by workboats, they routinely provide wear rates of 0.003" to 0.004" (0.075mm to 0.100mm) in 6000 to 7000 hours of annual use on the Mississippi River.
This upgrade was the first ship-assist tug in the New Orleans Port to change over to Thordon.
"We proposed retrofitting the RiverTough tailshaft bearing in conjunction with a ThorSleeve hardened shaft sleeve, and a TG100 shaft seal. This is a much more suitable shafting solution for vessels operating in abrasive rivers like the Mississippi,” Bright stated.
However, during discussions with the owner it emerged that a different installation method was required.
The traditional approach of casting Chockfast (an epoxy resin) directly to the outside diameter of the bearing meant that the Chockfast resin had to be chiseled out each time the existing rubber bearing needed replacing.
A new rubber bearing would have to be installed every 18-24 months. The bearing would have to be aligned and new Chockfast cast around them. This added to the time that the vessel was docked for repairs which in turn meant additional costs. When you factor the lost charter work into the equation, this process can be very costly for the ship owner.
Thordon’s solution was to create a permanent housing using the Chockfast epoxy grout.
Bruks Siwertell Group has announced a leadership transition as Peter Jonsson steps down as CEO after... Read more
ClassNK has issued an approval in principle (AiP) for a Rigid Windsail Type Wind-Assisted Propulsion... Read more
Elcome International’s new high-speed internet service, WELCOME, is revolutionising the way ship... Read more
Kaiko Systems, a leader in AI-driven frontline intelligence for the maritime industry, today announced... Read more
Marcegaglia’s latest acquisition, the LHM 600, marks a significant milestone as the 2,000th mobile... Read more
The Isle of Man Ship Registry (IOMSR) is playing a key role in the development of a high-tech sail aimed... Read more
AtoB@C Shipping, subsidiary of ESL Shipping, has taken delivery of Terramar in Goa, India on 14 March... Read more
As a new strategy period commences, VIKING Life-Saving Equipment A/S has achieved strong financial results... Read more
Baltic Exchange has introduced a series of green fuel options to its FuelEU voyage and compliance cost... Read more
Veson Nautical, a global leader in maritime data and freight management solutions, and Cargill have... Read more